For Danby and its customers, sustainability is very important. Every unit that is refurbished as “Danby Certified” helps to reduce the amount of recycling and waste being sent to a landfill, as well as lowers greenhouse gas production at our manufacturing plants. Our goal is to always work towards a more sustainable future.
Below are the steps we take in the remanufacturing process;
Returns
When a unit is returned to our warehouse, it is handled by our reverse logistics department. First, they unbox the unit and organize all the components. Then they inspect the products for any cosmetic issues.
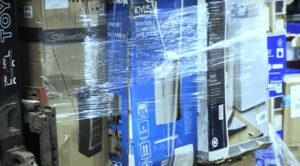
Testing
Products are put through rigorous testing to ensure they meet the original factory specifications and operate normally. However, if a component fails, then all gases are removed and collected safely. Additionally, all components are broken down and sent to recycling. This is very important in extending the useful life out of all our products. This also holds us at a high standard of quality, as the information gathered during the testing process can help us improve our designs for the future.
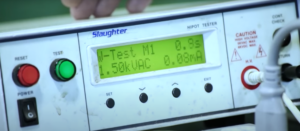
Remanufacturing
Products that pass testing receive a final cosmetic inspection where we can clean out all the components. Depending on the issue, the units can be painted and polished to resemble and function as a brand new product.
Reselling
All remanufactured units are then placed in brand new packaging and are sold a reduced cost. Our Danby certification also means that all remanufactured units will be sold with a 12-month warranty.
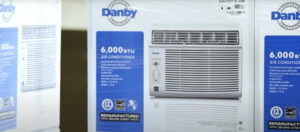
Find all of our refurbished product listings here!
Not yet following us on social media? Check us out on Facebook, Twitter, Instagram, Pinterest and Linkedin